一ã€Introduction of the structure features of the six-color printing machine The following picture is the NETER STAR2 six-color printing machine introduced by our company. It mainly includes the feed track, feeder, printing unit, coating unit, UV ink curing system, and online inspection device. , Receiving device and central control system. The technical parameters of the equipment are as follows:
Sheet thickness: 0.12-0.40mm Sheet width: 710-1200mm Sheet length: 510-1000mm Maximum production speed: 10.000/hr Its main features are:
1. Overprint accuracy, accuracy can reach 5um.
2. High degree of automation, production speed up to 10,000 sheets/hour 3. Replace single time short 4. The equipment runs smoothly
The following brief introduction METER STAR2 six color printing machine each part structure characteristic 1. Feida: It is similar to printing machine feeder, independent electric motor servo drive, the high precision synchronization guarantee, the automatic control iron plate arrival time; KUNZIMATIC positioning device: Pre-adjustment printing Positioning, front and side positioning using pneumatic suction device, rapid replacement of the side gauge on both sides (can run wave iron), change the side gauge less than one minute. It uses a unique iron sheet delivery method. Vacuum power supply, precision control below 15um, with patented technology.
2, VARISPEED positioning roller: intelligent tooth transfer device, to extend the transfer time of the printed sheet to ensure accurate transfer of the sheet at the highest speed. With the variable speed drum device, B+K uses two accelerations at the feed site to ensure a smooth transfer. The swinging tooth decays to 66% for the first time and then accelerates to 100% with the shift drum.
3. The unit: The automatic replacement of the job requires the use of fully automated technology. The process only takes 45 minutes. The working speed can reach 10.000 sheets/hour. Six printing units and one polishing unit are equipped with high-precision quality inspection and control facilities. The roller arrangement adopts the world-wide 7 o'clock method; the positioning accuracy of the feeding process is less than 15 um, the registration error between the units is less than 5 um; the double-diameter impression cylinder and the transfer drum design; the printing plate monitoring and positioning device; The power transmission of the unit is free from the horizontal axis transmission method in the past, and precision gear transmission can better ensure overprint accuracy. Newly designed guides, integrated cast iron stands, drum pretensioners and high-precision roller bearings, to avoid gear tooth gaps, vibration reduction, and high print quality at maximum speed.
4. Drum automatic cleaning device: The combination of three rollers (impression cylinder, blanket cylinder, plate cylinder) is cleaned by a combination cleaning device. It can automatically clean six groups of rollers at the same time, which takes about 10 minutes; When a traditional metal printing machine drum is changed, each group must be manually cleaned, and the time is about 10-15 minutes/time; in comparison, the preparation time is greatly saved.
5, automatic version of the device: the traditional metal color printing equipment are used manual or semi-automatic version of the device, and the introduction of equipment used automatic version of the device, it can six-color unit at the same time automatic version, this is a general It can increase the efficiency by about 5 times and reduce the labor intensity of employees.
6, cavity scraper system: printing plate positioning, on-line coating, to ensure that the local coating at high speed; on-line coating unit using chamber scraper and anilox roller device to ensure the quantitative supply of coating oil, can be saved Varnish dosage.
7. Iron plate pop-up detection configuration: Designed to meet the requirements of 10.000 sheets/hour; iron sheet can be re-entered into the machine; up to 200 sheets of iron can be collected.
8, UV ink curing system: 4 UV lamps, each only up to 160W/cm; energy to achieve stepless adjustment; can save energy.
9. Reclamation device: speed up to 10.000 sheets/hour, independent iron reducer.
10, the central control system: ERGOTRONTC center console, all the control keys can be digitally controlled, the job parameters can be easily replaced, and through the job call function, can greatly shorten the printing preparation time (can store 10,000 sets of printing jobs); Electronic standard components can be used throughout the world. The positioning system consists of radial, axial, and diagonal registrations. The ink zone control consists of each 30mm wide ink zone. Each ink zone does not interfere with each other. Online color control includes density and color difference. Based on standardized and convenient operation, automatic iron size setting, pressure control. Can control and adjust all basic printing parameters (such as ink volume adjustment, dampening fluid volume, register accuracy, print sheet size, cleaning program, etc.), and has remote diagnostic capabilities; can achieve CTP3 connectivity and computer direct and j version of the system ( CIF ); Reduce ink pre-adjustment time. Can integrate PRET CHECK3000 real-time quality monitoring system: single color registration, color tone classification, chromatic aberration and other issues can be monitored by the Print Check 300 system, monitoring the entire printed page color cast and registration, and can display diagnostic fault information, so that the printing staff in the emergence of Take precautionary measures before a large number of waste products.
Second, the introduction of UV printing ink printing operation points Because the UV ink printing ink has the characteristics of environmental protection, reduce pollution and increase production speed, it has the advantages of traditional printing ink incomparable. Therefore, most developed countries in the world have adopted this technology. In China, UV iron printing ink printing technology has just started in China. Shanghai Baoyin Metal Coating Co., Ltd. has introduced an internationally advanced high-speed six-color UV iron-printing machine from abroad, which has created a precedent for China's UV iron printing ink printing technology. Due to the relatively late start of the technology in this country, there has not been a set of perfect process flow, and it can only be explored on the side of production. By summarizing the problems in production and studying the experience of foreign counterparts of UV-chromium printing and consulting equipment and ink coating suppliers, the author came up with the following points of view for the people in the industry.
1. Make sure that the machine settings and pressure are in line with the normal requirements, glue, blanket and car wash water matching UV printing ink.
Since the binder of the UV ink is composed of an unsaturated acrylic monomer or a top polymer, this is not the same as the dissolution properties of the conventional heat curing inks (mainly alkyds). Unsaturated acrylic monomers are highly corrosive, which can cause erosion and swelling of the elastomer in the adhesive and blanket, and damage the photosensitive layer on the surface of the PS plate, resulting in the graphic off. Therefore, in the use of Yintie UV iron ink printing, must use special ink, ink blanket and car wash water for UV iron ink, PS plate must be high-temperature baking version, in order to enhance the image layer corrosion resistance. Related properties of adhesives and blankets are described below.
Roller: 25 - 40 Shore hardness EPDM rubber or PVC Nitrile rubber roll dampening roller: 25 Shore hardness EPDM rubber or PVC Nitrile (PVC Nitrile) rubber roller blanket: >70 Shore hardness EPDM rubber or PVC Nitrile blanket (Quick release type) Note: Use of EPDM rubber Be very careful not to use aromatic solvents (Naphtha, petroleum extracts) for cleaning 2. Make sure the fountain solution meets specifications.
Whether it is the traditional Indian iron craft or the UV iron craft, it is the key to control the balance of water and ink. The industry has a saying “Who knows how to control the fountain solution, whoever controls the printing†shows the importance of the visible ink balance to the printing. In the same way, the principle of less water, less ink and less water should be mastered. However, due to the special composition of the UV printing ink and its curing characteristics, it has stricter control over the ink balance than the traditional printing iron, and the range is narrower. See the following requirements in detail:
A. The fountain solution has a ph value of 4.8-5.2. If the dampening solution is too weak, it will cause printing problems, such as ink emulsification, stenciling, dirtiness, color deficiency, and dullness.
B. Set and control the level of isopropyl alcohol to 5-12%, depending on the water quality and additives used. In special cases, isopropyl alcohol consumption is even lower than 5% when using alcohol-reducing printing systems and high-sensitivity back-to-fine metering systems. Note: The most suitable wetting agent component is the shop concentration that reduces isopropyl alcohol consumption and minimizes evaporation of isopropanol near the printer.
C. Set the dosage of the dampening additive and ensure that the dampening has a lower and stable calcium town mineral content through the conductivity test, ideally, the indicator is 140-175 mg/L total hardness (Deionized water or reverse is highly recommended Permeate water plus 100-150 mg/L of minerals beneficial to printing (eg 0.50/o Emidamp fountain solution modifier).
Refer to the table of calibration icons D. The dampening fluid temperature should be controlled between 8 and 12 deg C. Inspection sequence:
(1) Each class passes the (thermometer) test temperature first,
(2) Test the isopropanol content by (liquid specific gravity meter),
(3) Then test the conductivity (in this order);
If the temperature exceeds the specification, it is necessary to adjust the "cooler" setting before measuring the conductivity because the temperature will affect the conductivity reading.
The isopropanol content should also be measured and adjusted before measuring the conductivity. (We recommend 7-10% for standard dampening additive (Emifount ULX). (Although different presses are slightly different)
If conductivity is too low, add more dampening additives (see figure) and re-setting feeders to compensate (Note: Most dosing feeders depend on a stable supply of water pressure to ensure accurate dosing).
If conductivity is too high but the dampening enthalpy is relatively fresh, then use water and alcohol to dilute and set the doser to compensate.
If the fountain solution is old, the conductivity will rise due to the contamination of the ink and the substrate. In most cases, a new fountain solution will be dispensed once a week.
3. Ensure that the attainable film weight is consistent with the color of the target.
Using the spectrophotometer, the target color (customer template) can be used as a reference, and excellent ΔE can be calculated by software. The maximum value of △E is set (for example, <5) for quality control. (Note: The opacity and hue of the white coating will affect the hue of light/deep browning, so it must be considered.) The four- and six-colour ink film should be controlled by measuring the density of solids on the color test strip. The film weight must not exceed the corresponding ink density value too much, otherwise it is easy to cause large ink, dirty version, poor curing and other failures. Six-color ink density reference values ​​are as follows (for reference only. Different ink systems or manufacturers, ink density values ​​may not be the same, but also with the matching presses):
Yellow ink density: 1.2
Magenta ink density: 1.4
The density of blue ink is: 1.4
Black ink density: 1.6
Orange red ink density is 1.5
The green ink density is 1.2
4. Perform the correct preparation procedure.
Maintain the lower ink film weight and fountain solution settings for each printing unit before positioning registration.
Once all plates have been correctly registered, slowly increase the film weight of the ink to reach the recommended reference density or color target.
Care should be taken in places where lower ink hiding power is used to avoid losing weight due to too rapid setting.
The fountain solution is still set to a low level, and then gradually increased to achieve an amount of water just enough to ensure that the non-graphic portion of the plate is clean.
When the proofs are acceptable, the machine can be accelerated and the fountain solution must be set to optimum.
5. Ensure that the UV printing ink has good adhesion with the primer.
Due to the inconsistent curing mechanism of UV printing ink and traditional printing ink, most of the primers suitable for traditional printing iron (white coating/bottom oil) are not suitable for UV printing. UV printing iron must be selected to adapt to the UV ink iron primer, in order to ensure that it has a good adhesion with UV iron ink, in order to meet the need for downstream processing of iron products. The method of checking the adhesion is the same as that of traditional stamping iron, and the tape method or nail scraping method is used.
6. Strictly implement maintenance and repair procedures.
(1) Strictly implement the maintenance and maintenance work of the printing machine pointed out in the manual.
(2) Replace the old fountain solution at least every week.
(3) Regularly check the output power of the UV lamp and replace it according to the manufacturer's recommendations. When replacing the UV lamp, clean the reflector at the same time.
a) Note: The staggered lamp replacement time ensures the most stable output.
b) It is recommended to check the UV lamp output power every few weeks to avoid poor curing (more advice on UV lamp monitoring can be obtained from the ink supplier).
(4) Remove calcium citrate deposits with a suitable roller cleaning paste every four to six weeks.
3. Application of computer-to-plate technology at Baoyin Company With the development of science and technology in the pre-press field, the application of direct plate-making machines has brought a qualitative leap to the plate-making industry. The plate-making system is a comprehensive multidisciplinary technology industry. It includes intelligence machinery and optical technology, electronic technology, color digital image technology, computer and software technology, new type plate and material technology, automation technology and network technology. Automatic production system.
Our company's prepress system has not adopted the traditional plate making technology since its establishment. Instead, it uses the CTcP direct plate making technology. This is also one of the few in the printing industry. It is a bold initiative in the printing iron industry in the country.
<1> Our Prepress Workflow Customer Original – Text, Image Processing – Separation Settings – Imposition – Save as EPS File – RIP into 1-Bit Tiff Rasterization File – CTcP Plate Making Plate development.
II. Working Principles and Imaging Characteristics of CTcP The working principle of CTcP is as follows: In the CTcP process, UV is irradiated to the DMD (digital micromirror device). There are more than 1 million micromirrors on the surface, and each micromirror is digitally processed. For control, the micromirror is like a pixel and forms a screened image on the plate. The exposure head of the CTcP system is very accurate, ensuring that images can be seamlessly stitched together after several consecutive exposures with an accuracy of 2 microns and an exposure speed of 10 exposures per second.
CTcP has another feature. The exposure technology it uses is a very small square dot (pixel). The dot size is between 10 and 28 microns. The sharpness of the dots obtained by the printing version is excellent. Even with lower resolution, CTcP can be used to obtain high quality images. The latest digital dot imaging technology ensures the synchronization of the exposure of the printing plate and the movement of the exposure head. Thanks to the US DSI2 technology, the exposure head can be continuously moved while the plate is exposed. This "continuous movement" technology prevents the exposure interval (when the head is moved) and ensures the high efficiency of the exposure of the printing plate.
<3) The advantages of CTcP: CTcP has many advantages. The most obvious is to improve the production efficiency, save time and reduce production costs.
1. The traditional printing plate satisfies both parties CTcP means "computer-made traditional plates." Our CTcP platesetters operate in the wavelength range of 360-450nm, so we can use traditional plates of good quality and durability to expose them. Plate making. The traditional printing plate manufacturing technology is mature and the quality is stable. It not only ensures the image quality, satisfies the requirements of customers, but also reduces the cost of our company. This is something that both parties are satisfied with.
2. Improved plate-making quality With direct plate-making, images and dots are not affected by the quality attenuation in the traditional pre-press process. The print quality of the printed matter has been significantly improved and the positioning is more accurate. Through technical tests, we compared the imaging results of different platesetters in the past: The square pixels produced by our company's CTcP are clearly lined at the FM network point and 50% amplitude modulation network point, and the edge of the network is sharp. Other plate-making machines, such as thermal and violet laser types, show signs of blurring edges due to the difficulty in controlling dot gain, which will result in a loss of quality in the final printing.
3. Higher work efficiency The computer-to-plate technology completely abandons the filmmaking process and reduces the possibility of man-made mistakes. It avoids the loss of the traditional film-printing outlets and makes prepress work easier and faster. Our CTcP platemaking machine can be flexibly combined with prepress equipment to provide a personalized solution. For different manufacturers' traditional printing plates, including UV plates, we can adjust the corresponding exposure parameter settings in advance. This process is simple and convenient, easy to operate, and it is almost impossible to adjust the settings of these parameters to complete the corresponding printing. Version of the exposure, truly "one for all."
4. Printing customers are more satisfied Customers are more satisfied with the quality of printed matter, printing production time is shorter, delivery is more timely, and the operation of the factory is reduced, making the printing company take the lead in fierce market competition.
Eppendorf tip refill is designed, developed and produced to perfectly match most brands of pipettes. The refill tower tip is suitable for most brands of pipetting systems to ensure pipetting accuracy. The sterile refill tower Pipette tip uses medical-grade plastic packaging to protect the Pipette Tips from contamination. The pipette tip refill is sterile, free of DNA, DNase, RNase, endotoxin or ATP. It can be autoclaved at 121 °C/250 °F (2bar) and sterilized by heat and humidity, in accordance with DIN EN 285. Environmentally friendly packaging. According to the IVD Directive 98/79, it has the European Union CE mark.
Compared with ordinary carton packaging, the refill tips system can save 60% of laboratory space and 70% of plastic. Without touching the tips, you can refill the shelf with one hand. Refill Pipette Tips can be used with universal carrier boxes.
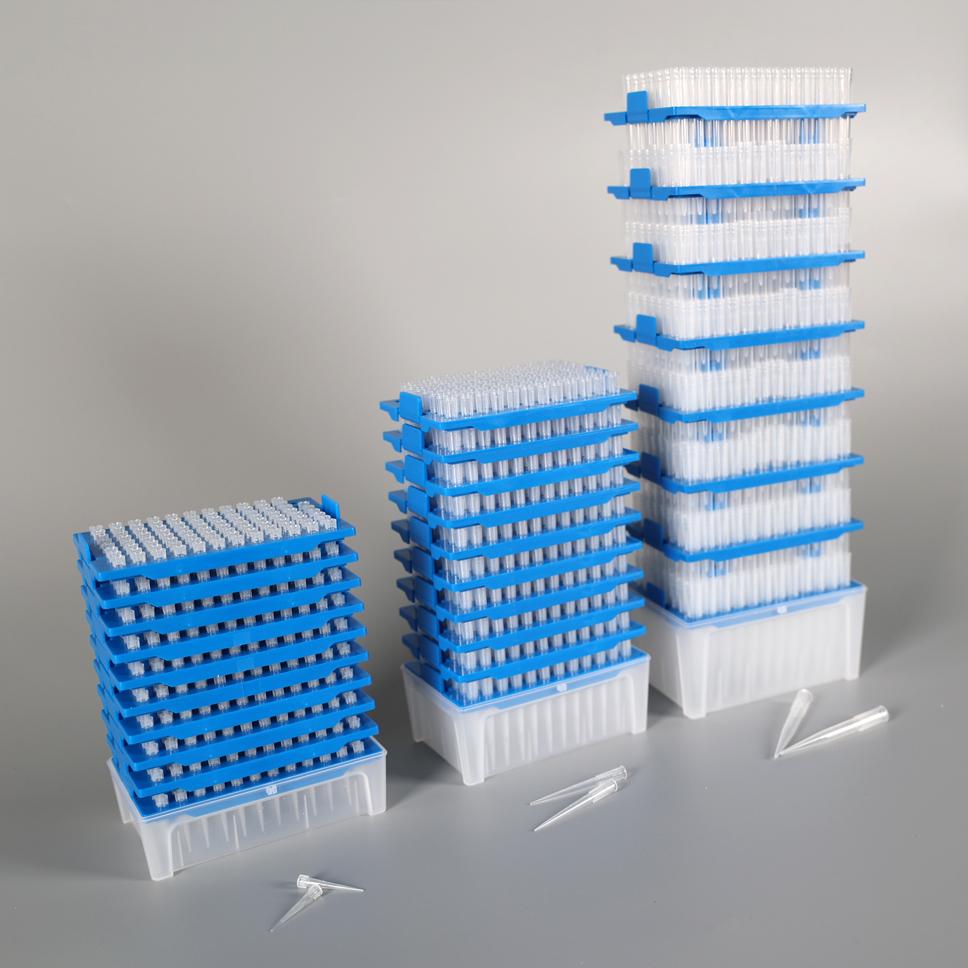
Pipette Tip Refill System,Pipette Tip Refills,Refilling Pipette Tips,Pipette Tip Refill,Pipet Tip Refill system
Yong Yue Medical Technology(Kunshan) Co.,Ltd , https://www.yypcr.com