Buffer beds are widely used in mining, power plants, cement plants, coal washing plants, etc. The advantages of buffer beds have been recognized by major industries, and actual customers often use buffer beds and belt conveyors to purchase or through their respective suppliers. The procurement of line buffer beds, the technical requirements of the quality, performance and design concept of the buffer bed are only a conceptual thing for most suppliers. At the same time, there are many transportation machinery factories that have certain equipment design experience. In order to reduce the cost, it is only a blind reference design, and there is no related mechanical analysis. The result is that the actual design of the buffer bed can not meet the actual needs of the customer. In severe cases, the impact of the material is too large, causing the buffer bed to be smashed. The bad question, they do not understand the true meaning of the "triple buffer" of the buffer bed design, and the consequence of this is often that the design of the buffer bed does not meet the actual needs of customers. The design and manufacture of buffer beds involves disciplines such as mechanics and engineering machinery manufacturing. Many transportation machinery factories have experience in engineering design, but they do not have experience in buffer bed design and application. Many customers only purchase buffers to reduce costs. Article, self-designed buffer bed processing production, but their design can not really start from the actual use point of view, to meet the actual needs of customers, and the buffer bed design should fully consider the conditions and stress analysis according to the actual customer use blanking point conditions With special design, Rita's cushion bed design concept is based on different design schemes for different conditions in different regions. Rita Rubber has long cooperated with international companies to develop, design and manufacture buffer beds earlier, with systems. Sexual design and related experience, there are many problems in the middle. In order to help the majority of users solve the problems encountered in the design and use of the buffer bed, we will analyze the reasons for the buffer bed instead of the buffer roller and the advantages of the buffer bed. To help customers understand and analyze the reasons.
1. The quality of the cushioning roller causes the tearing of the belt: the quality of the cushioning roller causes the tearing of the belt. Although our country has relevant national standards for the cushioning roller, the technical standards adopted by different suppliers are different, and the quality level is not uniform. It affects the use of buffer rollers; on the other hand, some suppliers of buffer rollers are often transport machinery factories. They do not have all aspects of performance testing standards for buffer rollers, and some buffer rollers themselves are unqualified, buffer rollers. The hardness of the surface rubber is too large and the quality is poor. Under repeated repeated impact conditions, the buffer roller will be damaged in a short period of time, and the cushioning roller also becomes a direct hidden danger of tearing of the conveyor belt. For example, the supporting roller has poor cushioning force, which can not absorb the strong impact force when the material falls, and easily damages the support shaft, causing the longitudinal tearing of the belt. 2, frequent stress, resulting in the support frame deformation, resulting in safety hazards: in some harsh conditions, the support frame is often subject to material impact and deformation, the roller is easy to fall off, the support roller upright bracket seat is easy to hang or Tearing the belt. In the case of Rita Rubber, there is a blanking height of 10 meters, a belt speed of 2.5m/s, a diameter of 500mm or more of iron ore, and a capacity of 800t/h. It will last for more than 3 months, because of its large impact force, which often causes tearing of the belt, and its maintenance cost is high. This situation is obviously improved after using the buffer bed designed by Rita.
3. The installation direction of the roller: the supporting roller and the conveyor belt are in line contact, and the two rollers are suspended between the two rollers, which are easily penetrated by the material or other sharp objects between the two rollers, and are stuck in the roller and the material port. Between the resulting belt penetration tear. The spacing and arrangement of the buffer bed is also scientific. When the sharp object is smashed into the buffer strip, the buffer strip wear layer-ultra-high molecular weight polyethylene sheet has excellent characteristics to withstand the impact force, so that the block can Continue to advance in parallel, and when the block hits the buffer strip gap, it will go forward in parallel due to the intermediate spacing, thus avoiding tearing of the belt due to the buffer roller blocking.
4. The roller is drooping and the sealing performance is poor: the belt between the rollers is easy to sag, so that the belt in the gap of the material is undulated, so that the sealing of the material is not good, resulting in material scattering and environmental pollution. Because the belt is running, it has to pass several transfer points, and the friction of the roller during the running process is easy to cause the belt to shift. The cushioning roller itself is spaced, and the idler time presents a "blocking distance". However, a wave shape is present, which is uneven in the buffer zone, causing a certain waste of resources and environmental pollution caused by the scattering of the block. The buffer bed adopts the principle of parallel force, and the force is relatively uniform, which is not easy to cause the block to be scattered. Big problem.
5. The quality of the buffer roller is poor, the surface of the supporting roller is inelastic, the surface is easy to adhere to the material for a long time, and the belt is worn. In severe cases, the belt will be deflected, and the supporting roller bearing will be impacted for a long time, and the bearing and the seal will be easy to fail. Causes the rotation of the tray body to be inflexible or not rotating, and the surface of the belt is worn. In the traditional conveying system, the friction and uneven force of the conveyor belt and the idler are more likely to cause the belt to run off. Especially in the rubber of the poor quality buffer roller, the friction coefficient is larger, which is easy to cause the belt. Severe deviation, and the "shun design" of the buffer bed plus the wear factor of the ultra-high molecular weight polyethylene sheet, which is a low friction coefficient material, greatly reduces the belt deviation caused by the friction with the conveyor belt. On the other hand, it protects the wear of the conveyor belt and prolongs its service life. Therefore, the buffer bed is the optimal support buffer structure for the material transfer point. Since the contact between the surface and the surface of the conveyor belt is ensured, the force is evenly distributed, and the longitudinal tear of the belt due to the breakage and falling off of the roller is effectively prevented, and the belt is greatly reduced. The penetration of the belt by the iron or sharp material leads to the probability of tearing of the conveyor belt, while the buffer bed core component buffer strip itself has a high elastic rubber cushioning, so that this problem can be well avoided.
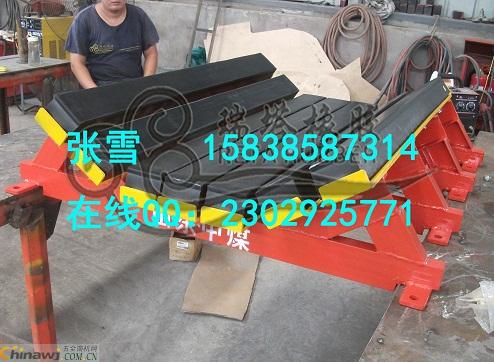
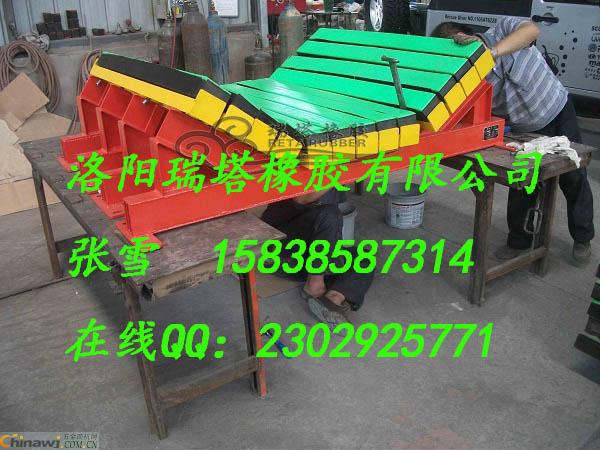
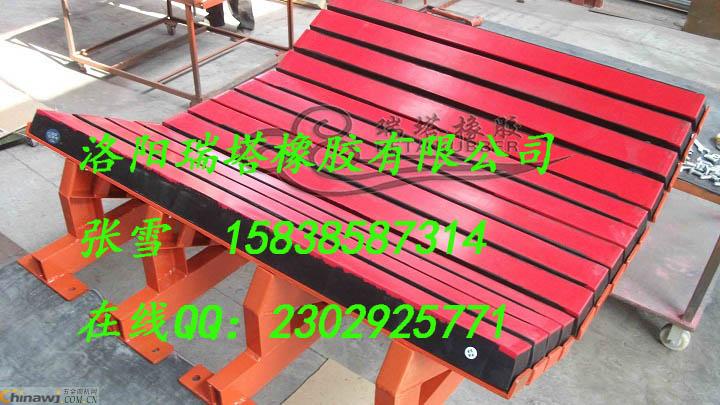
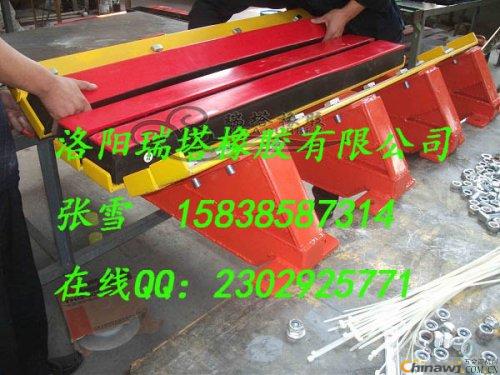
Characteristics and Advantages
(1) Intelligent control design: adjustable main parameter and secondary parameter automatically according to the weight of door leaves;
(2) Low noise: Special static sound track, integration of motor, worm-gear and retarder.
(3) Anti-clamping function: automatically reverse when meeting barriers;
(4) Unique electronic motor lock: the motor will lock up when the door is forced to open.(controlled by remote or switch)
(5) Tighten force: seal door when closed, power consumption approximately 10W under standby;
(6) Advanced brushless motor(36V,100W) can automatically adopt different heavy door leaves;
(7) Bi-doors inter-locking: one of the door leaves always remains closing;
(8)Safety sensor terminal: sensor stops working when door closed;
(9)Unique coating technology: never rusty;
(10)Easy and convenient to install;
(11)Working Process: when the door leaf closes to the right place, the door leaf will slightly shift to the door frame and the ground. The rubbers on the four sides of the door leaf will completely combine with door frame and ground, which ensures air tightness. When the door is open, the rubbers will separate from door frame and ground, which avoids contraction on the ground.
Technical Specification
Specification |
Light Duty |
Heavy Duty |
||
Rang of the Door |
Single-Leaf |
Double-Leaf |
Single-Leaf |
Double-Leaf |
Door leaf max weight |
100kg |
100kg x 2 |
200kg |
200kg x 2 |
Mounting Method |
Surface mounting or built-in mounting |
|||
Open Width |
700-2000mm |
650-2000mm |
750-2000mm |
650-2000mm |
Power Supply |
AC 220v ± 10%, 50-60 Hz |
|||
Opening Speed |
300-500mm/s (adjustable) |
|||
Closing Speed |
250-550mm/s (adjustable) |
|||
Creep speed |
30-100mm/s (adjustable) |
|||
Hold-open time |
0.5-20s (adjustable) |
|||
Airproof Force (Max.) |
>70N |
|||
Manual Pushing Force |
<100N |
|||
Electronic Lock Force |
>800N |
|||
Power consumption |
150W |
|||
Ambient temperature |
-20+50 C |
Technical Details:
(1) Rubber lining sealing technology combined with V groove on the guide rail enables the door completely sealed when the door closed;
(2)Special door body location technology. Semicircular surface beam on the ground matches with the V style groove at the bottom of door leaf, which stop the door from swing and make sure it moves stable and smooth;
(3) The door body decorated with matte stainless steel or spray surface, and on the middle and both sides with sealing stripes to ensure the hermetic effect.
(4)Feet sensor switch applied to avoid contagion;
Stainless Steel Sliding Door,Stainless Steel Bypass Sliding Door,Stainless Steel Interior Sliding Door,Stainless Steel Folding Sliding Door
Shenzhen Hongfa Automatic Door Co., Ltd. , https://www.hfautodoors.com